Sejarah
Didirikan tahun 1928, Motorola menjadi dikenal luas kareba radio dan produk elektronik dan listrik konsumen lainnya. Pada tahun 1960-an, perusahaan ini menjual produk dan semikonduktor, peralatan komunikasi, dan komponen kepada pelanggan, perusahaan industry, dan militer diseluruh dunia.
Dengan kantor pusat di Schaumburg, Illionis, pada tahun 1984, Motorala mencapai penjualan lebih dari $ 5,5 miliar, memperkerjakan lebih dari dari 99.000 orang, dan membelanjakan $411 juta untuk riset dan pengembangan. Perusahaan ini merupakan salah satu dari sedikit perusahaan Amerika yang memasarkan berbagai produk elektronik, dari integrated circuits (IC) yang sangat canggih sampai produk elektronik konsumen.
Perusahaan diorganisasi sepanjang lini produk dan teknologi. Setiap unit bisnis disusun sebagai sector, kelompok, atau divisi, tergantung pada ukurannya. The Semiconductor Products Sector (SPS) bermarkas besar di Phoenix, Arizona; penjualan pada tahun 1984 lebih dari $2,2 miliar, yang berarti 39% dari penjualan neto Motorola. Sektor itu menjual produknya di seluruh dunia kepada pabrik-pabrik peralatan asli melalui tenaga penjualannya. Produk semikonduktor selaras dengan perubahan yang cepat dalam teknologi. Oleh karena itu, SPS memelihara program riset dan pengembangan delam teknologi semikonduktor yang maju.
PEMBENTUK DIVISI ASIC
Untuk secara penuh mengeksploitasi permintaan yang tumbuh untuk IC, Motorola mengorganisasi Divisi Application Specific Integrated Circuit (ASIC) sebagai bagian dari Semiconductor Products Sector pada tahun 1984. Pada tahun 1985, divisi ASIC menempati fasilitas Chandler yang dimiliki Motorola, paling baru dari lima lokasi area-Phoenix yang dimiliki oleh perusahaan itu. Secara khusus, Motorola bekerja secara erat dengan pelanggan untuk mendesain semicustom IC. Walaupun demikian, beberapa desain dianggap sebagai desain standard an tetap hanya tersimpan sebagai barang persediaan.
Departemen Rekayasa Produk
Rekayasa produk berinteraksi dengan pelanggan dan menjalankan peran sebagai troubleshooter dalam menangani keluhan pelanggan. Ini adalah tanggung jawab aspek teknik dari manufaktur produk yang berkelanjutan. Para insinyur ditugaskan pada satu produk atau lebih dan melayani pelanggan untuk produk-produk ini. Bila pelanggan mempunyai keluhan tentang IC, rekayasa produk merespons perminyaan tersebut. Oleh karena itu, rekayasa produk adalah antarmuka (interface) teknis antara perusahaan dan pelanggan untuk produk yang ada.
Departemen Perencanaan Produk
Departemen perencanaan produksi dan departemen pelayanan pelanggan menjadwalkan pesanan dari pelanggan. Departemen ini memberitahukan pabrik kapan memulai produksi dan kapan produk yang telah dikerjakan harus selesai. Karena Motorola tidak memiliki sistem perencanaan produksi yang terkomputerisasi, kerja ini dilakukan hanya dengan software mikrokomputer standar, seperti spread-sheet. Pesanan harus ditelusuri secara manual melalui dari bawah (lantai pabrik). Ketika produk dikirim, departemen membebani ongkos kepada klien dan melaporkan informasi ini kepada pengendali keuangan.
Departemen Pemasaran
Departemen pemasaran bertanggung jawab untuk mengidentifikasi prospek awal dan melakukan penjualan kepada mereka. Tambahan pula, departemen pemasaran mempunyai tanggung jawab tertentu atas penetapan harga produk dan meramalkan permintaan pasar secara akurat.
Departemen Pengembangan produk baru
Kelompok pengembangan produk baru bertanggung jawab atas penjabaran spesifikasi produk pelanggan ke dalam desain yang dapat diproduksi dan untuk produksi prototype tersebut. Kelompok tersebut menyediakan estimasi biaya manufaktur pada kelompok pemasaran. Setelah desain selesai, estimasi biaya dijernihkan; ini dimasukkan dalam rencana implementasi produk, bersama dengan syarat hasil. Sebelum desain produk dapat diserahkan kepada departemen manufaktur, produk dibuat dalam area pengembangan pabrikasi dengan peralatan produksi. Pada tahap ini, proses harus harus memenuhi spesifikasi hasil minimum. Hasil ini bukan hasil yang diestimasikan dalam menghitung biaya manufaktur jangka panjang dari produk itu, tetapi merupakan hasil yang akan memuaskan ketika produksi bergerak cepat turun ke kurva belajar. Kurva belajar diestimasikan sekitar 70 persen untuk kebanyakan produk dalam divisi ASIC. Kurva belajar 70 persen berarti bahwa biaya unit untuk volume produksi total akan berkurang dengan 30 persen setiap waktu volume produksi kumulatif menjadi dua kali.
Departemen jaminan kualitas
Quality Assurance (QA) atau departemen jaminan kualitas bertanggung jawab atas kualitas produk secara terus – menerus Tes visual / mekanis lebih subjektif. Cacat pada area ini dapat dikarenakan salah cetak, cetakan tidak terbaca , komponen yang pudar, atau kabel timah yang bengkok. Banyak dari cacat ini tidak mempengaruhi kelayakan rangkaian tetapi hanya mempengaruhi penampilan visualnya. Salah satu tanggung jawa QA adalah menyampaikan kepada manufaktur apa yang merupakan penolakan produk tersebut.
QA memiliki pelatih-pelatih yang berdiskusikan dengan operator manufaktur tentang apa yang menjadi penolakan. Progam ini memilik dua manfaat (1) operator menjadi sadar bahwa mereka perlu memproduksi tingkat kualitas tertentu ; dan(2) bila produk di bawah kualitas yang dapat diterima pada suatu tahap dalam produksi, ini akan segera ditolak oleh operator ; oleh karena itu lebih menghemat biaya manufaktur.
Departemen Manufaktur
Departemen manufaktur terdiri dari pekerja upah per jam, supervisor, dan staf rekayasa pabrik. Pekerja upah per jam terlibat langsung dalam mengoprasikan mesin produksi dan menginspeksi kerja-dalam-proses. Departemen manufaktur mempunyai tugas untuk menjaga kesinambungan proses produksi dan metode yang digunakan dalam perakitan dan untuk pelaksanaan pengetesan. Focus kelompok ada pada proses manufaktur, dan bukan pada produk spesifik.
Pasar ASIC
Dalam pasar semicustom IC, pelanggan menciptakan desain dari “bagian-bagian pembentuk” (building blocks) yang disediaakan oleh para perancang Motorola. Keterlibatan oleh pelanggan di tengah siklus pengembangan ini berbeda dengan keterlibatan dalam produk semikonduktor lain yang ditawarkan oleh Motorola. Motorola menyediakan jasa desain bagi pelanggan dan mengelola hubungan pelanggan yang terlibat secara relative. Oleh karena itu, organisasi Motorola berfokus pada pelanggannya, dan bukan pada produknya.
Pelanggan divisi ASIC secara khusus adalah pabrik-pabrik computer, seperti DEC, Apple Computer, Unisys, Cray, dan Prime Computer. Pelanggan-pelanggan ini bersaing di pasar yang ditandai dengan perubahan teknolgi secara cepat dan perkenalan produk baru secara cepat juga. Mempersingkat waktu pengiriman produk merupakan kepedulian utama bagi mereka. Kualtas tinggi, waktu pengembangan cepat, dan kemampuan untuk mencapai produksi volume secara cepat penting sekali dalam memenangkan bisnis pelanggan-pelanggan ini. Dibandingkan dengan faktor-faktor ini, harga memiliki adalah prioritas kedua.
Beberapa pelanggan, seperti Hewlett-Packard, mengembangkan system manufaktur just-in-time (JIT) dan menyatakan kebutuhan mereka untuk pengiriman tepat waktu dan komponen yang masuk berkualitas tinggi.
Sistem Manufaktur dan Akuntansi Motorola
Sebelum bergerak, divisi ASIC merupakan bagian dari sector korporat lain. Produksi bipolar, sebelum bergerak, menggunakan system manufaktur dan akuntansi yang ada pada Motorola. Dalam pabrik, mesin dan pekerja di organisasi sepanjang garis funsional. Setiap mesin dikendalikan sebagai bagian dari kelompok fungsi, dan secara fisik dekat dengan mesin lain yang melakukan fungsi serupa. Desain fungsional ini menghasilkan gerakan fisik produk yang besar pada jarak yang relative besar pada lantai pabrik (produksi tingkat bawah). Setiap bagian yang dimanufaktur mempunyai jalur yang ditentukan melalui pabrik itu.
Dalam desain pabrik ini, ada 29 pusat biaya, yang persediaannya dinilai pada biaya standar. Persediaan dikelompokan menurut tahap penyelesaian untuk proses penetapan biaya. Penjaluran (routing) produk melalui pabrik secara khusus meliputi langkah – langkah sebagai berikut: (1) suku cadang, dimana berbagai bahan mentah dibeli dan dipersiapkan; (2) pabrikasi lembaran tipis ( wafer), dimana wafer silicon yang mengandung logic array diproduksi; (3) die (blok potong), dimana wafer dites dan dipotong ke dalam rangkaian individu atau chip dan dipasang pada substrate paket (permanent chip enclosure); (4) perakitan, di mana kawat timah dipasang pada chip dan pengemasan diselesaikan; (5) tes, di mana chip yang dikemas dites menurut spesifikasi pelanggan; dan (6) barang jadi, di mana produk yang dikemas untuk dikirim.
Sistem ini memerlukan banyak pencatatan. Entry dibuat setiap waktu produk dipindahkan dari satu pusat biaya ke pusat biaya lain. Audit fisik yang dilakukan atas inventory diperlukan untuk menelusuri dan membuktikan kebenaran jumlah produk.
Bahan, buruh, dan standar overhead diperbaharui dua kali setahun. Walaupun demikian, standarnya sering kali usang, karena lingkungan dinamis dan kurva belajar yang tajam. Overhead dialokasikan pada produk atas dasar buruh langsung. Buruh langsung secara cermat ditelusuri untuk dapat menetukan biaya buruh pada produk dan untuk menyediakan alokasi overhead pada produk itu. Manajer manufaktur mengestimasikan bahwa diantara 8 persen dan 12 persen dari waktu produktif karyawan dihabiskan dalam membuat catatan.
Buruh langsung dibayar menurut system upah per jam dan bonus. Bonus kebanyakan ditentukan oleh perbandingan jam buruh langsung actual dengan jam buruh standar untuk setiap karyawan.
Desain fungsional pabrik mengakibatkan kesulitan dalam menempatkan tanggung jawab atas produk individu. Petugas ekspedisi dalam departemen perencanaan produksi melakukan tugas penting dalam menjamin bahwa produk yang penting dapat diselesaikan secara tepat waktu. Walaupun demikian, pabrik itu terhambat oleh waktu proses yang lambat. Manajemen merasa bahwa waktu penyelesaian IC terlalu lambat, dibandingkan dengan perusahaan-perusahaan jepang yang bersaing.
Desain fungsional juga menghasilkan jumlah persediaan besar dan batch yang besar. Ukuran batch yang besar menghasilkan persediaan barang dalam proses di antara stasiun fungsional dan menghasilkan persediaan barang jadi yang secara efektif dihasilkan tetapi mungkin tidak diinginkan oleh pelanggan.
Banyak orang merasa bahwa, bukannya membantu manajer menghadapi kompleksitas system manufaktur, system akuntansi sebenarnya memperbesar masalah. Pengendalian divisi mencatat, “Kesadaran penting yang pertama dari departemen akuntansi adalah bahwa kami kadang kala menjadi perintang untuk maju. System akuntansi menhasilkan kegiatan disfungsional keseluruhan dan menghambat gerakan pada teknik manufaktur baru.”
System biaya standar merepotkan dan tidak dipahami secara jelas oleh karyawan pabrik. Karyawan pabrik mengalami kesulitan dalam mengikat varians pada masalah spesifik. Karena varians tidak menunjukkan masalah actual, maka solusi a priori pada varians sulit ditentukan. Pekerja pabrik khusus beranggapan bahwa laporan varians tidak relevan dan oleh karena itu mengabaikannya.
Ketidaktepatan waktu juga merupakan masalah. Biaya standar dihasilkan setiap bulan. Kurangnya umpan balik harian atau mingguan membuat sulit mencari penyebab varians yang tidak menguntungkan. Varians bulanan merupakan akumulasi banyak kegiatan yang menguntungkan dan tidak menguntungkan, yang tidak diidentifikasi secara khusus oleh analisis varians. Buku ditutup pada hari kerja ketujuh setelah akhir bulan. Tujuh hari kerja tambahan diperlukan untuk menghasilkan laporan biaya actual dan varians. Pada waktu laporan diterima pada lantai pabrik, departemen manufaktur baru setengah jalan melalui periode akuntansi yang lain.
PELUANG UNTUK BERUBAH
Manajer divisi ASIC yang baru saja terbentuk menyadari bahwa pembukaan sebuah fasilitas produksi baru di Chandler mempresentasikan kesempatan untuk memperkenalkan perubahan pokok dalam operasi manufaktur divisi tersebut. Oleh karena itu, tata letak lantai pabrik baru itu dirancang secara khusus agar sesuai filosofi JIT dan dengan proses spesifik pabrik tersebut. Satu manajer pada tapak pabrik Chandler menyampaikan pendapat bahwa mereorganisasi fasilitas fungsional yang ada untuk melaksanakan pabrik yang menganut JIT itu jauh lebih sulit.
Pabrik itu diorganisasi di sekitar Sembilan sel: (1) persiapan perakitan; (2) perakitan 72-pin; (3) perakitan 149-pin; (4) perakitan lain; (5) penyegelan, pengetesan mekanis, dan pemberian merek; (6) pemanasan (heat sink); (7) burn-in (pemotongan dangan nyala gas); (8) pengetesan dan pengepakan produksi; dan (9) penggudangan dan pengiriman. (Tampilan 2 adalah diagram tata letak pabrik). Tidak semua produk melalui semua sel-misalnya, tidak semua chips memerlukan heat sink. Walaupun demikian, semua chips yang dihasilkan oleh pabrik Chandler itu diproses dalam sebagian besar sel yang ada.
Produk bergerak dari sel ke sel dalam urutan yang ditunjukkan dalam Tampilan 2. Wafers (masing-masing terdiri dari sejumlah chip) ditempatkan dalam die cage (tempat blok pemotong) ketika sampai pada pabrik tersebut. Dari die cage, wafer diambil pada sel persiapan die, di mana gate arrays pada wafer yang belum dites pada fasilitas pabrikasi wafer dicek dengan alat pemeriksa untuk menentukan deretan-deretan mana yang baik. Deretan-deretan yang tidak lolos inspeksi dilemparkan keluar.
Kemudian, chips diambil pada satu dari tiga sel rakitan (72-pin, 149-pin, lain-lain), tergantung pada family produk dan jumlah sambungan yang diperlukan untuk dibuat pada chips tersebut. Dalam sel perakitan, dibuat sambungan listrik pada chip tersebut. Dalam penyegelan (sealing), pengetesan mekanis, dan sel pemberian merek, chip disegel dalam kemasan pelindungan, dites dan ditandai untuk identifikasi. Dalam sel ini, beberapa chips bervolume rendah dibengkokkan dari arus produk normal ke dalam lini opsi khusus. Garis ini adalah untuk IC dengan volume yang sangat rendah, yang biasanya dibuat untuk pelanggan yang menggunakannya untuk prototype dan pengetesan. Focus dari opsi ini adalah waktu penyelesaian yang cepat; untuk beberapa IC, satu lusin atau lebih dapat dikirmkan dalam tiga minggu dari saat desain diterima. IC dengan volume lebih tinggi disalurkan melalui sel selebihnya. Seperti yang telah disebutkan di atas, tidak semua IC dikirim ke heat sink dan sel pembakaran, tetapi ke heat sink dan sel burn-in, tetapi semua melalui sel tes, sel pergudangan, dan sel pengiriman.
Kebanyakan dari proses tersebut dijalankan dengan mesin, dan kebanyakan pemesinan bersifat kompleks dan mahal. Ini secara khusus benar bagi assembly dan test cell. Misalnya, mesin tes yang diotomatiskan pada akhir biaya lini opsi di atas $2 juta masing-masing.
Masing dari sel tersebut dijalankan oleh tim produksi, yang diawasi oleh seorang pemimpin tim. Arus kerja dikendalikan melalui system tarik (pull), dengan area yang direncanakan dengan persediaan terbatas diizinkan di antara stasiun kerja. ( system manufaktur tarik dicirikan oleh produksi yang berfungsi bila persediaan dipindahkan dari persediaan barang jadi ). Bila area penyimpanan di depan stasiun kerja penuh, stasiun sebelumnya harus tetap menganggur. Salah satu dari sel perakitan didiagramkan dalam tampilan 3. Dalam sel ini, chips digabungkan pada bagian bawah dari permanent enclousure (kemasan) dalam stasiun blok pemotong (die bond station), dan bergerak melalui seperti yang ditunjukkan oleh anak panah; operasi final yang dilakukan dalam sel melekatkan kabel timah dalam stasiun sambungan kawat (wirebond stations). Sel-sel tersebut dirancang sedemikian rupa sehingga produk bergerak masuk ke satu arah sepanjang jalur yang berbentuk huruf U.
Peran Sistem Pengendalian Manajemen
Pengendali Divisi ASIC secara akut menyadari kecenderungan sistem penegendalian yang usang dan yang berlaku untuk menghalangi kemajuan dalam operasi manufaktur. Ia merasa kuat sekali bahwa kantornya seharusnya tidak semata-mata berdiri di sampingnya tetapi harus mengambil posisi positif dalam mendorong perubahan-perubahan di seluruh divisi itu. Walaupun demikian, ia bertanya-tanya jenis sistem pengendalian manajerial manakah yang akan melengkapi dan bahkan mengarahkan perubahan-perubahan progresif yang terjadi dalam operasi divisi tersebut.
sejarah perkembangan motorola
Beberapa Produk Denture, untuk produk yang lain silahkan bisa konsultasi ke customer service di 085293424149
Cara Pembelian Produk Denature
TATA CARA PEMBELIAN:
Smskan alamat atau konsultasi, jika tertarik > transfer pembelian > barang dikirim pake TIKI/JNE/POS kealamat rumah. No.rekening via sms atau ada di bawah ini
Silahkan lakukan Pembayaran terlebih dahulu ke salah satu rekening BANK kami dan barang kami kirim melalui Jasa pengiriman Tiki / JNE / POS.
CARA PEMESANAN :
Silahkan lakukan Pembayaran terlebih dahulu ke salah satu rekening BANK kami dan barang kami kirim melalui Jasa pengiriman Tiki / JNE / POS.
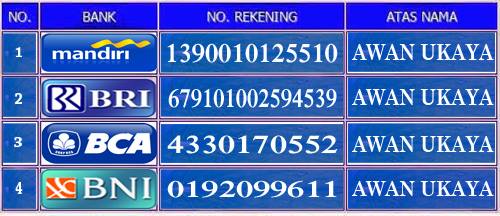
FORMAT PEMESANAN:
Bambang, pesan Gonore, Jl Kenari No 90 RT09 RW08 Kelurahan karangsari Kecamatan Bongsari, Semarang 52537 – Jawa tengah via MANDIRI
Kirim ke no : 085293424149
CONTOH KONFIRMASI PEMBAYARAN:
Bambang, Telah Transfer Rp. 340.000, – , Via MANDIRI, Obat Gonore
Konfirmasikan Via SMS ke : 085293424149
* Perhatian :
– Jika Transfer dari rekening orang lain harap disebutkan nama pemilik rekeningnya
– Paket dikirim rapi dan tidak menyebutkan nama penyakit
Untuk Biaya Kirim/Ongkir Di sesuaikan alamat pemesan :
- Untuk Wilayah Pulau Jawa Rp 25.000,-
- Untuk Luar Pulau Jawa Rp 45.000,-
- Khusus Untuk Irian Jaya dan Madura Rp 85.000,-
- Untuk Ongkir Luar Negri Silahkan Call / WA 085293424149
Agar pesanan Anda bisa segera diproses, segera konfirmasikan pembayaran Anda via SMS ke 085293424149
- Jika anda masih kurang jelas silahkan kontak kami langsung via Tlp/Sms 085293424149
- Barang DIJAMIN sampai ke rumah anda dengan catatan nama dan alamat lengkap.
- Hubungi kami apabila menginginkan bukti nomor (resi) pengiriman.
Jangan Sampai Anda mengajukan pertanyaan seperti ini???
- Mas, nanti kalau saya transfer uangnya, barang tidak datang atau tidak dikirim bagaimana???
- Mas, ini penipuan bukan??? Sekarang kan banyak penipuan???
- Saya kan tidak kenal situ??? Masa saya transfer ke situ? kenal juga ngga???
Bukti Resi Pengiriman dan Paket Rapi
Sekarang jaman Online Bos, kita disini sudah terbiasa belanja Online. Sekarang
sudah Jaman Modern, sudah jaman internet, bukan jaman perjuangan lagi.
Tinggal beli, tunggu barangnya dirumah. No.resi pengiriman saya smskan.
Cek resi pengiriman di www.jne.co.id atau di Tiki www.tiki-online.com
sudah Jaman Modern, sudah jaman internet, bukan jaman perjuangan lagi.
Tinggal beli, tunggu barangnya dirumah. No.resi pengiriman saya smskan.
Cek resi pengiriman di www.jne.co.id atau di Tiki www.tiki-online.com
SEPARAH APAPUN PENYAKIT YANG ANDA DERITA DAPAT DISEMBUHKAN JIKA ANDA MAU BERUSAHA MENGOBATINYA !
Silahkan jangan ragu untuk mengontak nomer kami
Call/SMS/WA : 085293424149
PIN BB : 7A68E8B4
Call/SMS/WA : 085293424149
PIN BB : 7A68E8B4